When considering the enhancement of poultry processing systems, one often overlooked yet vital component is the scalding tank. This piece of equipment is essential for efficiently loosening feathers on harvested poultry, a step critical to maintaining quality in subsequent processing stages. A well-designed scalding tank ensures that processing operations unfold smoothly, bolstering productivity while upholding stringent quality standards.
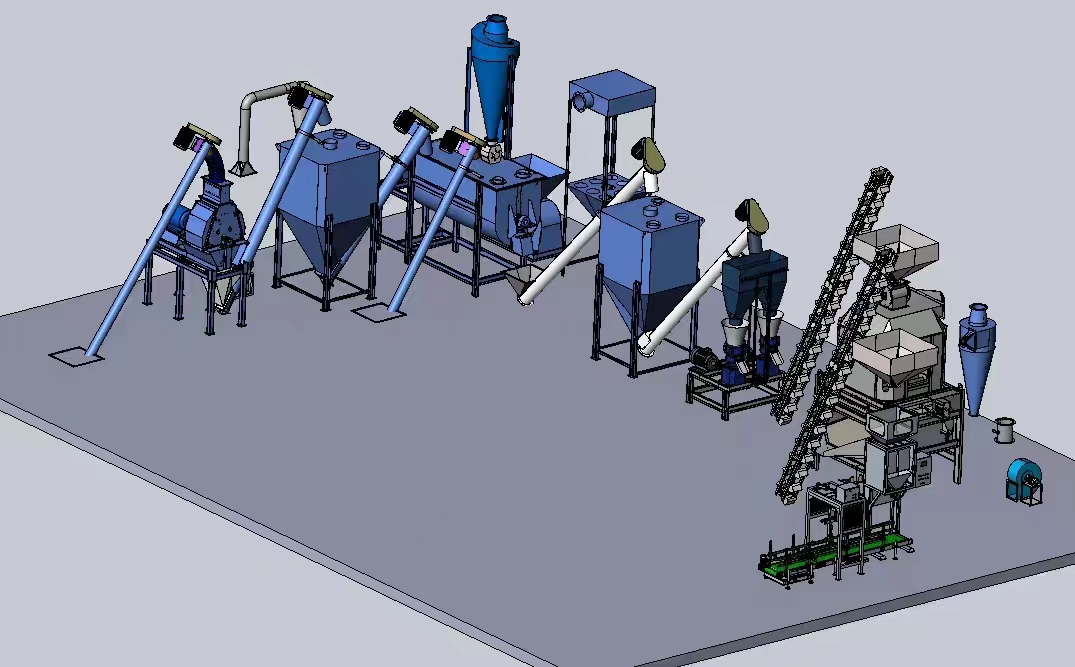
A professionally-constructed scalding tank is characterized by its ability to maintain consistent water temperatures and flow. These factors are crucial because they directly affect the ease with which feathers can be removed. Operating at optimal temperatures - generally between 50-60 degrees Celsius, depending on the type of poultry - ensures that the outer skin loosens feathers without damaging the underlying skin. Such precision not only facilitates a faster plucking process but also minimizes the risk of quality degradation, which is paramount for maintaining consumer trust.
Expertise in the field underscores the need for advanced materials and technology in scalding tank construction. Stainless steel is typically the material of choice, offering durability,
easy sanitation, and resistance to corrosion. High-grade stainless steel ensures longevity and prevents contamination, safeguarding consumer health, and supporting regulatory compliance. An intelligently-designed tank also incorporates energy-efficient heating elements and water-saving features, which not only reduce costs but also contribute to environmental sustainability, an increasingly important consideration for consumers and regulators alike.
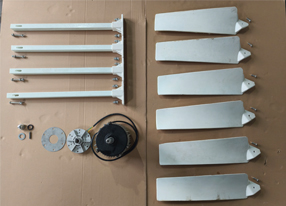
The authoritativeness of a scalding tank system can also be gauged through its integration with automated controls. Modern scalding tanks often feature digital interfaces that allow operators to easily adjust temperature settings, monitor water flow rates, and manage maintenance schedules. Real-time data collection and analysis provide valuable insights into system performance, facilitating proactive maintenance and early identification of potential issues that could lead to operational disruptions. Such technological advancements reflect the cutting-edge nature of modern poultry processing, ensuring that operations remain competitive and viable over the long term.
scalding tank
Trustworthiness in scalding tank selection and operation hinges on adherence to industry regulations and standards. Buyers and operators should prioritize models that comply with international standards, such as those set by the International Organization for Standardization (ISO) and local health departments. Certifications from recognized bodies not only demonstrate a commitment to quality and safety but also bolster consumer confidence in the final product. Additionally, manufacturers often provide comprehensive training and support, enabling operators to maximize the utility and lifespan of their equipment.
In terms of real-world experience, users frequently report significant improvements in processing time and product quality post-implementation of advanced scalding systems. Testimonials from poultry processors often highlight reduced manual labor requirements, enhanced control over processing parameters, and overall better workflow efficiency. Such experiences reinforce the value of investing in high-quality scalding technology as a means of achieving operational excellence and maintaining competitive advantage in the fast-paced agricultural sector.
In summary, the integration of a well-designed scalding tank can dramatically elevate the efficiency and quality of poultry processing operations. By focusing on factors such as material quality, technological sophistication, and compliance with industry standards, processors can ensure that their operations consistently produce high-quality products. Such commitment to excellence not only boosts productivity and cost-effectiveness but also reinforces a brand’s reputation for reliability and quality in the marketplace.